削る世界の名職人 古澤 利明
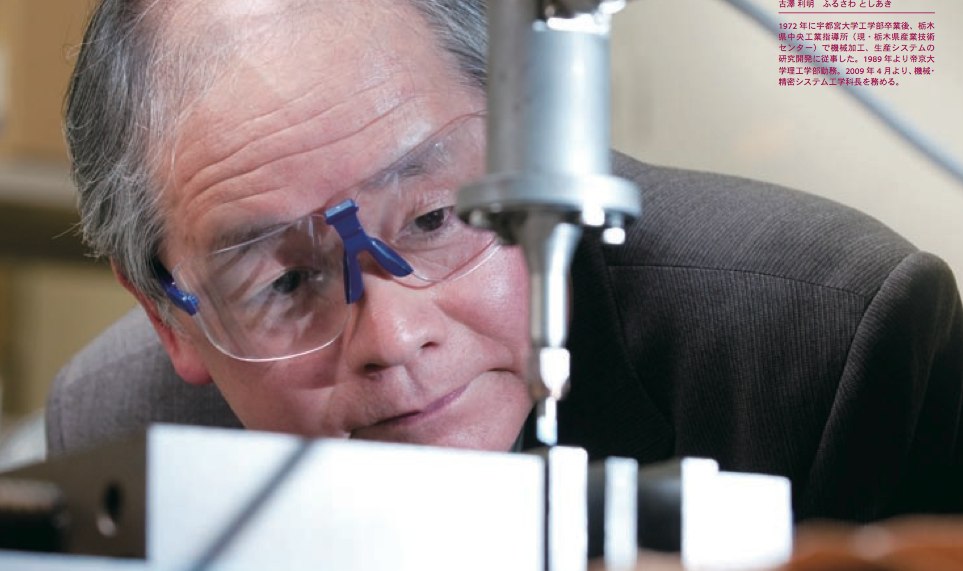
年々小型化していく機械。
コンピュータも、原型ができた 1940 年代は 教室くらいの部屋がひとつ必要なくらい大きな機械だった。 機械が小さくなっていく裏側には、 小さくても十分に能力を発揮できるようにする努力がかくされているのだ。 古澤先生の加工技術は、微小世界の医療の未来をより便利にする可能性を秘めている。
金属加工の匠
古澤先生の研究室で行っているのは、数cm程度の金属材料に1mm以下の穴や溝をつくり出す技術の研究。
穴を開けるといっても、小さな世界となると簡単なことではない。
丸い穴ならまだしも、六角形など少しかたちが違うものになるとその難しさは格段に上がる。
丸い穴なら、ドリルなどの工具を使って掘り進んでいけば開けることができる。
しかし、六角形の穴を掘るとなると、ドリルを使うわけにはいかない。
回転させながら掘っていくと、先が三角であれ四角であれ、できた穴は丸になってしまうからだ。
大きい穴ならば、初めに丸く穴を開けて、その穴の周りを削り、かたちを徐々に三角や四角にしていくことは可能だが、小さい穴で同じことを行うのは、使用する工具の大きさから考えても非常に難しい。
実現するには、経験豊富な職人の知識と腕が必要だ。
古澤先生たちは、穴と同じかたちの工具を振動させて削る方法をとっている。
これを1cmの500分の1という、肉眼では振動しているのかどうかわからないほどの幅で1秒間に20000~40000回振動させ、工具の先端を金属に押し当てながら削っていく。
その名も「超音波振動切削」。
切削とは、工具を金属に押し当てて表面を削り取る方法。
ものづくりの中では、部品どうしのつなぎ目やガソリンなどの液体の通り道をつくるときに活躍している技だ。
他の大学でも超音波で切削を行う方法は研究が行われているが、特殊なかたちをした穴の削り方については、古澤研究室だけのオリジナルの技術だ。
チーム栃木
生まれも育ちも宇都宮。
大学と就職先まで栃木県内という古澤先生は、生粋の栃木人だ。
この土地で生活してきたからこそ、今の専門分野にも出会えた。
宇都宮大学卒業後に就職した県の中央工業指導所(現・栃木県産業技術センター)でたまたま配属された先が、現在の専門である切削を行っていた。
大学では、金属が部分的にもろくなる金属疲労という現象の研究を行っていたが、始めてすぐに削る技術のおもしろさに惹き付けられた。
「そりゃおもしろいですよ。特に1mm以下のかたちを思った通りにうまく削れたときは、やった!と思います」と語る笑顔には、現場でたたき上げてきた努力と、思い入れがあふれている。
そして現在、栃木県にある帝京大学理工学部を舞台にして、全国に誇れる加工技術の開発に挑んでいる。
そのために、県内の企業と最高のものづくりができるチームも結成した。
地元にある工具をつくる企業、自動車の重要部品をつくる企業、精密部品に通じた企業、超音波発生に必要な部品をつくる企業とコラボレーションして、最高のものづくりが進んでいる。
医療の未来を担う技術
研究を進めるうえで、成果が世の中の役に立つかというのは重要な課題。
問題が起きている現場に自ら出向いて、そこから課題を見つけ出して研究を行い解決策を社会に教えていく研究者がいれば、現場を理解している企業と共同で研究を行い、お互いに足りない部分を補いながら世の中で役に立つ技術を生み出していく研究者もいる。
地元企業とチームを組んで技術開発を行っている古澤先生は、後者に当てはまる。
現在は、企業の研究者だけでなく、学生もメンバーに加えた共同研究で医療技術の未来を担う加工技術の開発に取り組んでいる。
「実際にプロジェクトに関わることで、理論ばかり追うのではなく、今世の中でどういった加工技術が求められているかを把握できる人材として成長できる点は、工学の分野では特に重要です」と古澤先生は言う。
自分たちでつくり上げた技術の応用に向け、帝京大学医学部と連携した。
微小血管を縫い合わせる手術に着目し、時間との勝負である手術において、それを補助する微小器具を開発し、医師の負担を軽減させようとするものだ。生体に使用可能なチタン材料の微小加工が現在のテーマとなっている。
六角形の穴を掘る技術は、この開発で活かされようとしている。
「削ることのおもしろさは、うまくいかないこともあるけれども、自分で削ったときのイメージをふくらませて、その通りにできたときにあります。
私の打率は2割くらいだけれども、うまくできたときはとにかくうれしい」と、笑顔で語る古澤先生の研究は、医療技術の進歩に大きく貢献できる可能性を秘めている。